在制造業蓬勃發展的浪潮中,生產方式正經歷著前所未有的變革。傳統的手工上下料模式,曾經在生產線上發揮著重要作用,但如今已難以適應高效、精準的現代化生產需求。尤其是在對精度和效率要求極高的 CNC 加工領域,手工上下料的弊端愈發凸顯,不僅效率低下,還存在諸多安全隱患和精度問題,成為制約企業發展的瓶頸。?
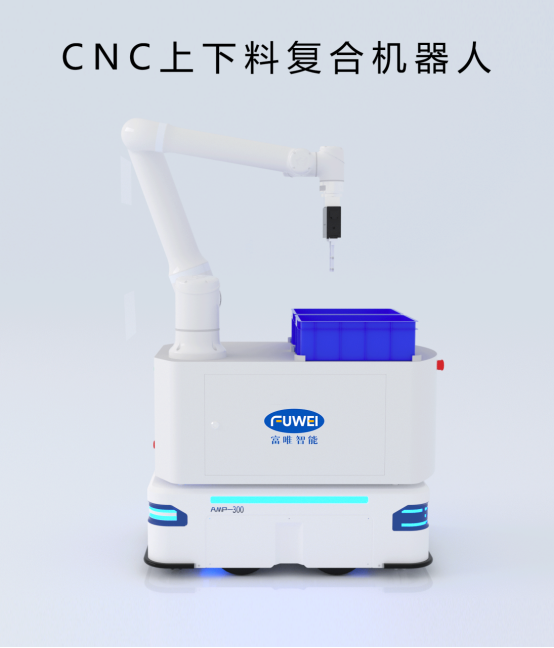
工藝現狀與需求
該企業現有CNC加工生產線采用手工上下料方式,工人需將產品裝配到治具上,再將治具連同定位臺一同搬運到CNC設備內進行加工。加工完成后,再由工人取下產品并轉移至成品區。這種方式不僅勞動強度大、效率低下,而且容易受人為因素影響,導致加工精度不穩定。
企業希望實現CNC加工生產線的自動化上下料,提高生產效率、降低勞動強度,并確保加工精度。
?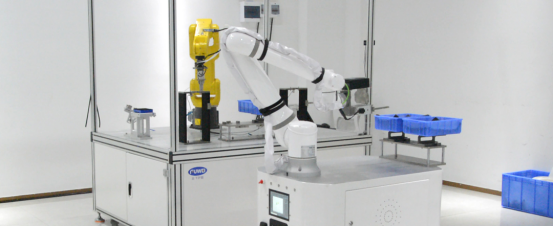
解決方案
1. 復合機器人AMR:采用2臺AMR復合機器人進行上下料作業,具備高精度抓取、放置功能,能夠實現與CNC設備的無縫對接。
2. 視覺識別系統:采用富唯視覺識別軟件ForwardVision,對Mark標進行高精度識別,確保機器人抓取和放置的精度。
3. 自動充電系統:AMR機器人配備自動充電樁,實時監測電量并自動調度充電,確保24小時持續作業能力。
4. 通訊對接方式:機器人與CNC設備通過專用信號進行通訊,實現自動開門、關門、啟動設備等操作。
5. FRDS調度系統:對整個生產線進行高效調度和管理,確保機器人和CNC設備之間的協同作業。
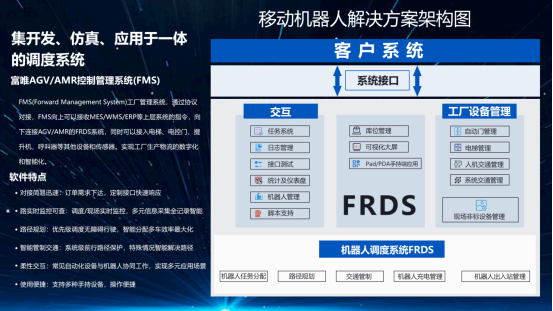
方案優勢
1. 高效性:復合機器人AMR能夠實現快速、準確的上下料操作,大幅提高生產效率。
2. 精準性:采用視覺識別系統和高精度抓取技術,確保產品放置誤差小于±1.5mm,滿足高精度加工需求。
3. 安全性:機器人具備自動避障、行人檢測等功能,確保生產過程中的安全。
4. 靈活性:系統可根據生產中心計劃實時調整生產狀態,適應不同產品的加工需求。
5. 可靠性:AMR機器人綜合放置成功率實現>99%,確保生產線的穩定運行。
?
實施效果
通過實施該解決方案,該制造企業的CNC加工生產線實現了自動化上下料操作,生產效率提高了30%以上,產品加工精度得到了顯著提升。同時,降低了工人的勞動強度和安全風險,為企業帶來了顯著的經濟效益和社會效益。
?
本案例展示了基于復合機器人AMR的CNC自動上下料解決方案在制造業中的應用效果。隨著智能制造技術的不斷發展,我們相信未來將有更多企業采用自動化、智能化的生產方式,提高生產效率、降低成本、提升產品質量。我們將繼續關注市場動態和技術發展趨勢,為更多企業提供優質的智能制造解決方案。