在當下競爭激烈的 CNC加工行業,人力成本的持續增長宛如一座沉重的大山,壓得企業喘不過氣來,成為制約企業發展的關鍵瓶頸。特別是在鋁板 CNC上下料這一關鍵環節,傳統的人工操作方式猶如一場效率低下的 “馬拉松”,弊端愈發明顯。
?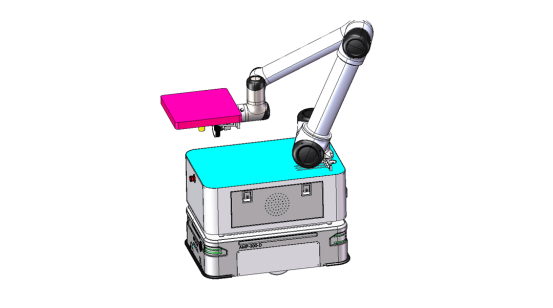
人工上下料需要大量人力投入,每一個工作班次都需要安排多名工人在 CNC機床旁值守,進行鋁板的搬運、定位和裝夾。這不僅使得企業的人力成本大幅增加,而且由于工人的體力和精力有限,長時間重復勞動容易導致疲勞,進而影響操作的準確性和穩定性。據相關數據統計,在傳統人工上下料模式下,因工人操作差異和疲勞導致的產品次品率高達 10% - 15%,生產效率也被嚴重拖慢,一條生產線每天的有效工作時長因工人休息和狀態調整等因素,平均減少 2 - 3 小時。
?
富唯智能憑借對行業趨勢的敏銳洞察力和深厚的技術研發實力,及時推出了 AMR 復合機器人鋁板 CNC上下料方案,為行業帶來了曙光。這款 AMR復合機器人堪稱科技融合的結晶,它巧妙地將協作機器人的靈活性、移動機器人的機動性以及視覺引導技術的精準性完美融合。其搭載的 ICD 系列核心控制器,猶如一顆強大的 “智慧大腦”,能夠對整個復合機器人系統進行全方位、一體化的精準控制,確保每一個動作都能按照預設程序準確無誤地執行。
?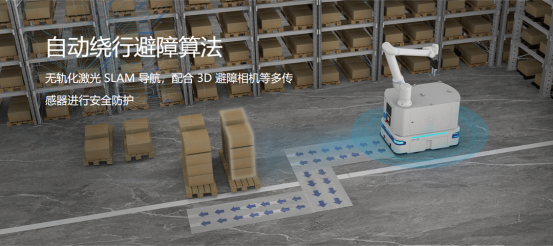
在鋁板 CNC 上下料的實際應用中,AMR 復合機器人展現出了無可比擬的優勢。借助先進的視覺引導技術,機器人能夠在瞬間識別鋁板的位置、姿態和尺寸信息,實現快速且精準的定位。隨后,協作機器人的機械臂會以極高的精度完成鋁板的抓取和搬運動作,將鋁板準確無誤地放置在 CNC 機床的工作臺上。整個上下料過程一氣呵成,不僅大大減少了人力投入,以往需要 3 - 5 名工人協同完成的工作,現在僅需 1 - 2 名工人進行監控和輔助即可,人力成本降低了 50% - 70%。
機器人的高精度操作和高效工作速度更是顯著提升了生產效率。在傳統人工操作模式下,每完成一次鋁板上下料,平均需要 3 - 5 分鐘,且由于工人技能和狀態的波動,上下料的精度難以保證。而 AMR 復合機器人完成一次上下料僅需 30 - 60 秒,且定位精度可控制在 ±0.1mm 以內,生產效率提升了 3 - 5 倍。同時,機器人具備穩定運行和長時間續航能力,能夠 24 小時不間斷工作,有效避免了因人工疲勞、休息等因素導致的生產中斷,確保了生產過程的連續性和穩定性,進一步降低了企業的運營成本。
?
值得一提的是,AMR 復合機器人還具備智能避障和自動讓行功能。在復雜的生產車間環境中,它能夠通過傳感器實時感知周圍的環境信息,當檢測到前方有工人或其他設備時,會自動調整運行路徑,靈活避讓,確保與工人之間的安全交互。這一功能不僅提高了生產環境的安全性,降低了因人為因素導致的生產事故風險。