項目背景
在當(dāng)今制造業(yè)自動化升級的趨勢下,本次項目聚焦于復(fù)合機器人 CNC 自動上下料領(lǐng)域。旨在通過先進的自動化技術(shù),實現(xiàn)對多臺 CNC 機床的高效上料和下料操作。在生產(chǎn)過程中,CNC 機床內(nèi)加工的產(chǎn)品先由操作人員整理放置于小托盤內(nèi)。這些裝有產(chǎn)品的小托盤需要通過自動化方式在 CNC 加工中心與其他區(qū)域之間進行流轉(zhuǎn),而 CNC 加工中心有特定的放置位置參數(shù),其高度為 1000mm,深度為 400mm,并且每臺機床的加工時間在 15 - 20min 之間。整個項目計劃使用 1 臺復(fù)合機器人完成對 8 臺 CNC 機床的上下料工作,這對來料和下料方式的規(guī)劃提出了較高要求。
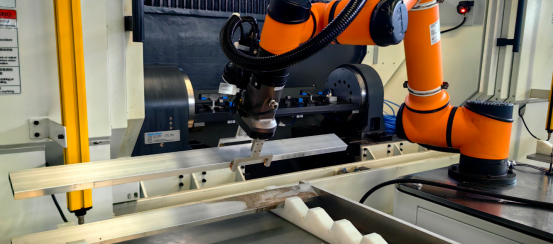
項目難點
1、上下料流程復(fù)雜
需要協(xié)調(diào)操作人員、轉(zhuǎn)運機器人、復(fù)合機器人以及輸送線等多個環(huán)節(jié),確保待加工產(chǎn)品從整理到上料,以及加工成品從下料到人工理料區(qū)的流程順暢且準(zhǔn)確。
2、定位與抓取精度要求高
復(fù)合機器人需要通過 3D 視覺和機器人夾爪對小托盤進行準(zhǔn)確的取出和放置操作,尤其是在 CNC 機床內(nèi)部有限的空間和特定的位置條件下,要保證高精度的定位和抓取,避免碰撞等問題影響加工效率和產(chǎn)品質(zhì)量。
3、多臺機床協(xié)調(diào)作業(yè)
1 臺復(fù)合機器人要服務(wù) 8 臺 CNC 機床,需要合理安排其在各機床之間的移動順序和時間,保證各機床的上下料需求都能及時響應(yīng),同時避免機器人在移動過程中的沖突和等待時間過長的問題。
4、來料和下料方式規(guī)劃
要考慮待加工產(chǎn)品和加工成品的來料和下料方式,確保物料在不同環(huán)節(jié)之間的有效轉(zhuǎn)接,避免物料堆積或供應(yīng)不足的情況。
解決方案
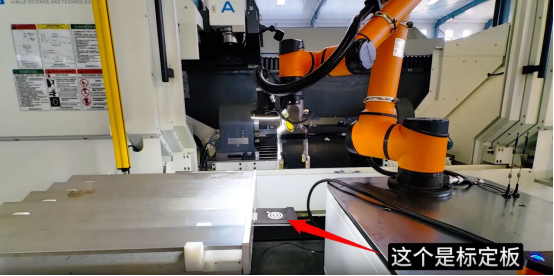
1、來料流程
操作人員將托盤上的待加工產(chǎn)品放置到輸送線大托盤的小托盤上。隨后,轉(zhuǎn)運機器人移動到輸送線接駁位,將待加工的大料盤接駁到自身。接著,轉(zhuǎn)運機器人前往對應(yīng)的 CNC 機床旁邊的上料料架接駁位,并將大料盤送入上料料架。
2、上料流程
復(fù)合機器人移動到 CNC 機床上料位,利用 3D 視覺 + 機器人夾爪的先進技術(shù),從已就位的上料料架上準(zhǔn)確取出小料盤,并將其放入 CNC 機床內(nèi),然后退出,為機床加工做好準(zhǔn)備。
3、下料流程
當(dāng) CNC 機床加工完成后,復(fù)合機器人移動到 CNC 機床下料位,再次借助 3D 視覺 + 機器人夾爪,將機床內(nèi)加工完成的小料盤取出,放置到 CNC 機床旁邊下料料盤的大托盤上,之后退出。
4、成品轉(zhuǎn)運流程
當(dāng)下料料盤滿料后,轉(zhuǎn)運機器人移動到 CNC 下料料盤接駁位,通過輸送線將滿料的加工成品大料盤接駁到自身,然后將其轉(zhuǎn)運至人工理料區(qū),完成整個加工成品的下料流程。
核心價值
1、提高生產(chǎn)效率
通過自動化的上下料流程,減少了人工操作時間和錯誤,并且復(fù)合機器人和轉(zhuǎn)運機器人的協(xié)同作業(yè)可以快速響應(yīng)多臺 CNC 機床的需求,大大縮短了加工周期,提高了整體生產(chǎn)效率。
2、提升產(chǎn)品質(zhì)量
復(fù)合機器人的 3D 視覺和高精度夾爪技術(shù)保證了上下料過程中的準(zhǔn)確性和穩(wěn)定性,減少了因人為因素或操作不當(dāng)導(dǎo)致的產(chǎn)品損壞,從而提升了產(chǎn)品質(zhì)量。
3、降低人力成本
原本需要大量人力參與的上下料工作,現(xiàn)在大部分由自動化設(shè)備完成,減少了對人工的依賴,降低了人力成本,同時也避免了因人員疲勞等因素對生產(chǎn)的影響。
4、增強生產(chǎn)靈活性
該解決方案可以根據(jù)實際生產(chǎn)需求,靈活調(diào)整復(fù)合機器人的工作路徑和轉(zhuǎn)運機器人的接駁順序,適應(yīng)不同的加工任務(wù)和產(chǎn)品類型,為企業(yè)的多樣化生產(chǎn)提供了有力支持。